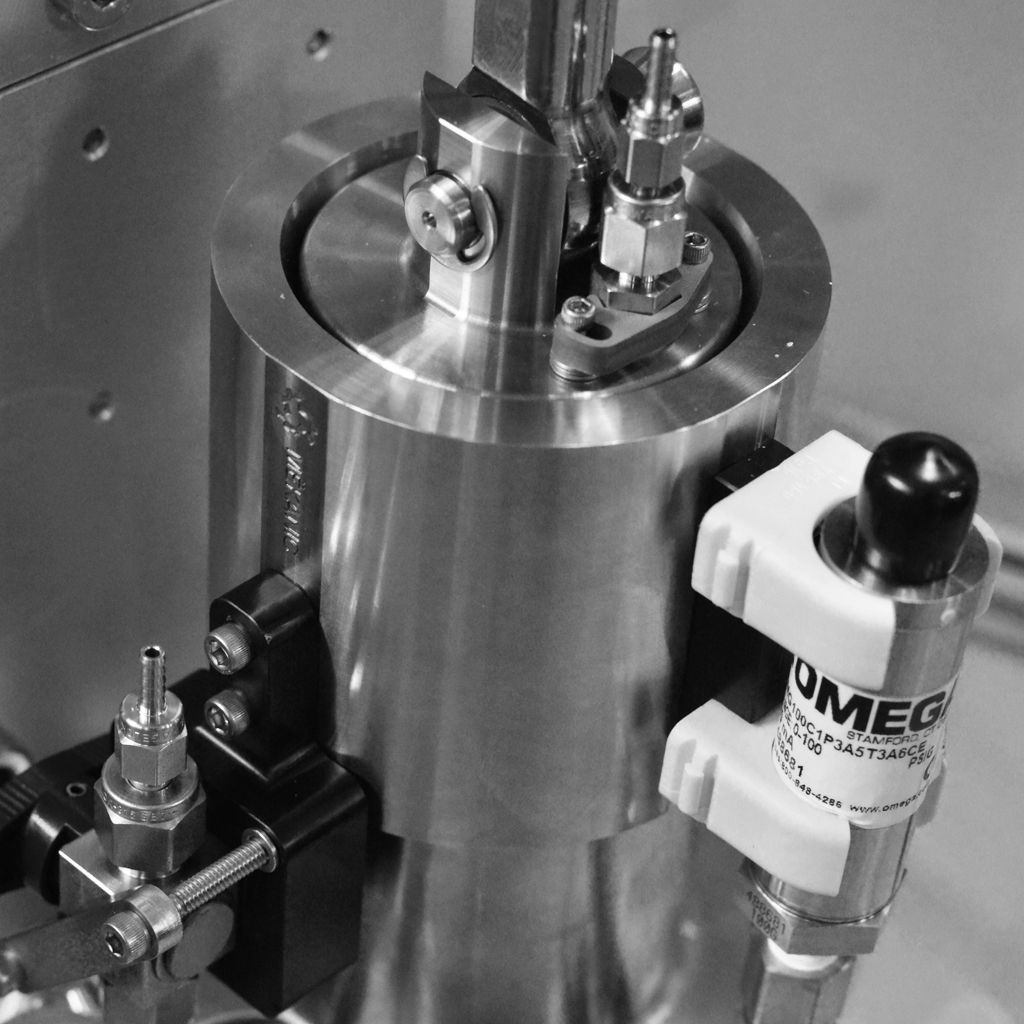
System for manufacturing ceramic composite aerospace materials
Sector
Aerospace / Composite Materials
Societal benefits
Develop new methods for making ceramic matrix composites. These materials are advantageous for applications in gas turbines and aircraft engines because they are lighter than the commonly used nickel superalloys and have better resistance to high temperatures. Engines containing such components may be more thermodynamically efficient and produce fewer emissions from an environmental point of view.
Mandate
Develop and manufacture a press to make ceramic/ceramic-fiber composites as part of a collaborative aerospace industry/university research project. It involves applying pressure to a mixture of water and ceramic powder, and filtering this liquid through a porous ceramic fibre membrane. The system is equipped with a robotic controller interfaced with a computer to perform the acquisition of experimental data.
Development time
7 months
Technological advancements
- Control flow mode and piston advance speed
- Precise control of electric cylinder at very low speeds
- Sealing for an extremely abrasive fluid
Scientific advancements
This equipment accurately measures the permeability of various porous media. It’s very important to define the operating parameters of the infiltration processes to produce the ceramic composite matrix. In addition, the Darcy cell piston can also be used as a high-precision injector for moulding parts of more complex geometries.
Specs
- Actuator: 500 lbf max. [225 N]
- Impregnation pressure: 100 psig max. [7.0 bar]
- Thickness of ceramic matrices to be impregnated: 0.040-0.250″ [1.0-6.5 mm]
- Volume of impregnation solution: 15 in3 [250 ml]
- Impregnation control in flow or pressure mode